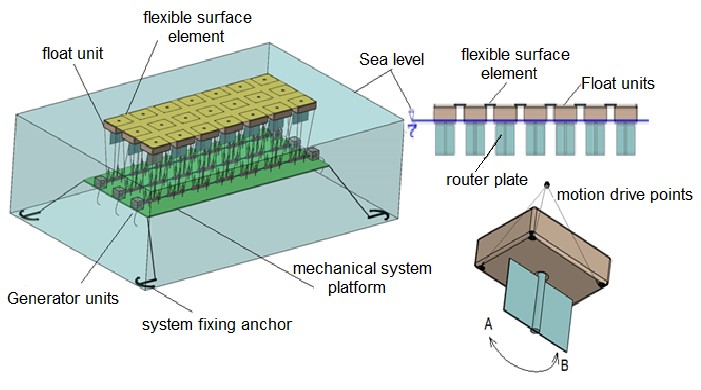
• In this new design, the flexible surface floats slightly above sea level depending on the floats, and the incoming waves are directed under the flexible surface by the buoys carrying the flexible surface.
• Under each float that carries the flexible surface, there are routers that can rotate around its axis (in the direction of A-B) with a wave effect, and which can generate channels under the flexible surface by rotating the routers at the bottom of the entire float.
• The direction of the wave to the system is not important, the wave is directed to the bottom of the flexible surface.
• Each float and the resilient surface have multiple drive points for transmitting the wave effects, so as to create several drive points along the resilient surface, all movements on the flexible surface have been attempted to be transferred to the mechanical loop.
• The in-depth length of the resilient surface is used as a control for the wave effect, the transmission of the wave power to the loop, a controlled power transfer is provided, the in-depth distance in the system is used as a time-saving parameter for us to transfer the wave power.
• The fact that the flexible surfaces and the buoys are not high above the sea level do not form a large resistance surface against the wave, so that if the wave cannot penetrate under the flexible surface at the unpredictable wave heights, it can easily go over the flexible surface without causing much resistance and destructive effect and does not damage the system.
• In this design, the platform carrying power shafts and generator units can be fixed by positioning them below sea level. Since the system is not obliged to use a cage system that is placed on the carrier floor, as it is seen in the figure, it has gained a suitable design for open sea applications.
• The design, which has become suitable for open sea applications, has gained an aesthetic structure visually.
• With this structure of the system, modular production provides easier transportation and assembly advantages.
• With this design, the system has become more suitable for both offshore and offshore applications.
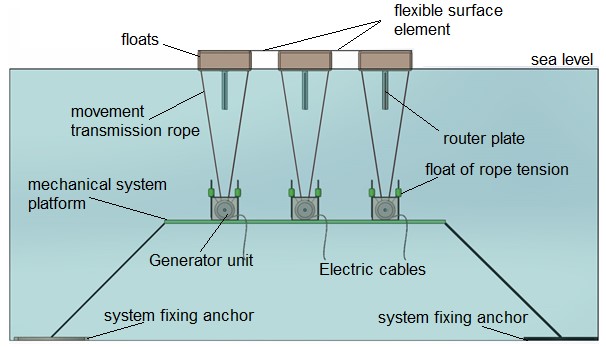
• In the design of this system, only flexible surface elements are seen on the sea surface.
The platform which is in the sea and the mechanical parts is partially floating and is immersed in the desired amount and fixed at the desired sea level by the sailor anchors. The application in this design allows the application of the sea depth at 20 mt or more.
• The platform which is in the sea and carrying the mechanical parts is partially floating and is immersed in the desired amount and is fixed at the desired sea level with the sailor anchors. The application in this design allows the application of sea depth at places 20 mt or more.
• Mechanical system elements inside the sea do not contain any materials causing marine pollution by creating oil and dirt in the marine environment. Some of the system elements are made of stainless material, some of them are composite materials, some of them are synthetic and seawater and they do not harm the environment. Some iron parts are painted with special paints against rust formation and precautions are taken so as not to pollute the sea.
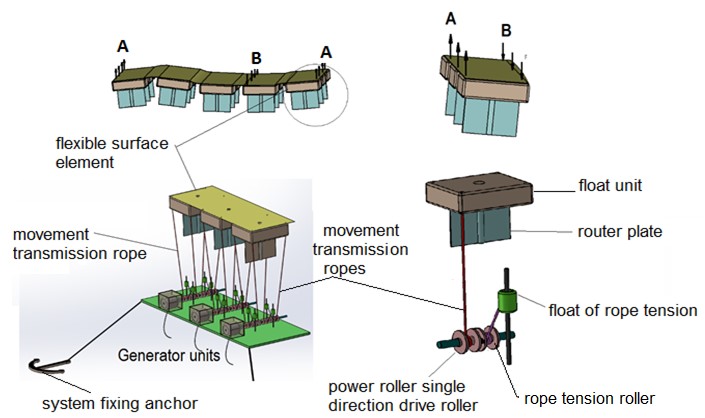
• The power transmission ropes connected to the float and the flexible surface swivel into the one-way pulley and allow the flexible surface movements moving with the wave effect to rotate to obtain energy from the power shaft.
• The buoys under the flexible surface and the flexible surface will cause a movement in the direction of B in the other part of the float while creating an upward movement in the direction A with the wave contact and the first contact of the wave. All wave effects under the flexible surface will cause different movements to be affected across the entire surface and at all surface points, and this interaction will continue in the period of progression of the wave under the entire flexible surface.
• Relative impacts in the A – B directions of the wave underneath the flexible surface previously described and continuing along the entire surface, and all of these movements are transmitted directly to the power shafts with one-way rollers without the need for much process steps with the help of power transmission ropes.
• These relative effects on the flexible surface with the effect of the wave effect, the movement at each flexible surface point affect the other flexible surface point near this point and cause a movement at this point, our attempt to catch all these movements with our many drive points is serious on system efficiency. contributes a contribution.
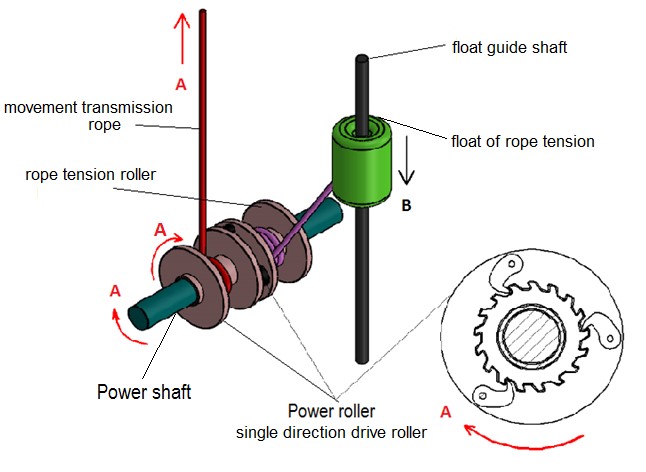
• Only one of the power transmission ropes connected to the float and the flexible surface is seen in the upper figure. The upward movement of the flexible surface with the wave effect will also pull up the power transmission rope connected to it in direction A. This movement of the power transmission rope will turn the unidirectional pulley clockwise in the direction A, and in this one-way pulley it will turn the power shaft clockwise (A) by means of gears which will enable one-way rotation of the power shaft.
• The rope tension roller connected to the unidirectional pulley and rotating with it will rotate in a clockwise direction during the real work period of the power shaft (along the upward movement of the flexible surface) and will pull it downward in the direction of the rope tension buoy B by means of the rope connected thereto. Since the rope tensioner buoy has a volume of swim ability, it will want to move towards the surface of the water continuously and this physical condition will always keep the power transmission rope with a certain tension by means of the rope and the rope tensioner.
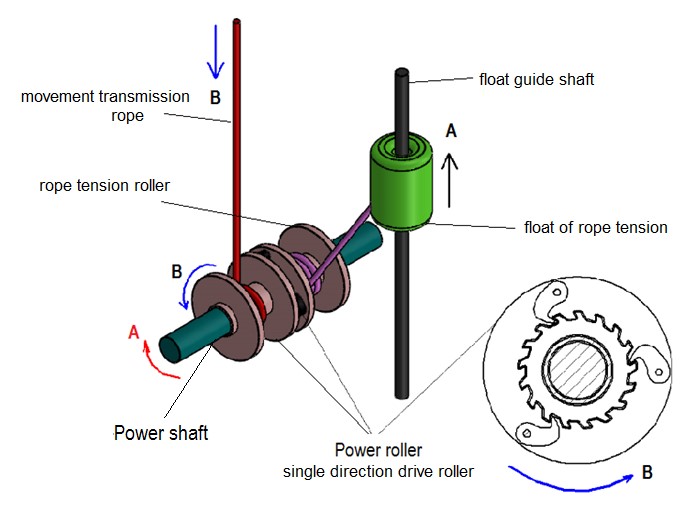
• During the progression of the wave under the flexible surface and the downward period of the flexible surface, the power transmission rope will tend to form a downward gap, so that the rope tensioning pulley and the rope tensioner can be used to ensure that such a gap does not occur and that the flexible surface is stretched to turn the power shaft even at the smallest upward movement. We use the buoy.
• It will move upwards in direction A with the buoyancy of the rope tension buoy in the absence of an upward pulling force on the power transmission rope. This upward movement of the rope tensioner buoy will cause the rope tensioning pulley and thus the unidirectional pulley to be turned into a tensioned state by rotating it counterclockwise in the direction of B by taking the blank of the power transmission rope.
• The toothed system on the one-way spool rotates in idle direction when rotating in the direction of the threaded system B, not forming a resistance, and allowing the unidirectional pulley to rotate in a non-resistive manner, allowing the transmission of the power transmission rope wrapped around it to be wound by means of the rope tension roller. Due to this feature of the unidirectional pulley and gear system, the power transmission rope at this driving point is stretched to produce power at the next effect as described.
• The power transmission rope at each drive point enables the power shaft to rotate clockwise in the direction A and generate electricity by means of wave action and flexible surface movement. The power transmission ropes that do not work effectively and are in vain will turn the power transmission rope to the unidirectional pulley and rotate without any counter-clockwise direction of rotation with the help of the rope tensioner buoy